This gearmotor is a powerful 12V brushed DC motor with a 70:1 metal gearbox and an integrated quadrature encoder that provides a resolution of 64 counts per revolution of the motor shaft, which corresponds to 4480 counts per revolution of the gearbox’s output shaft. The gearbox is composed mainly of spur gears, but it features helical gears for the first stage for reduced noise and improved efficiency. These units have a 16 mm-long, 6 mm-diameter D-shaped output shaft. This gearmotor is also available without an encoder.
Key specifications:
voltage |
no-load performance |
stall extrapolation |
12 V |
150 RPM, 200 mA |
27 kg⋅cm (380 oz⋅in), 5.5 A |
Overview
Measuring 37 mm (1.46″) in diameter, these brushed DC gearmotors are the largest and most powerful we carry. They are available in a range of gear ratios from 6.3:1 to 150:1 and with 12 V or 24 V motors, and all versions are available with integrated 64 CPR quadrature encoders on the motor shafts. The 12 V and 24 V motors offer approximately the same performance at their respective nominal voltages, with the 24 V motor drawing half the current of the 12 V motor. See the 37D metal gearmotor datasheet (2MB pdf) for more information, including detailed performance graphs for each gearmotor version.
Details for item #4754
This gearmotor is a powerful 12V brushed DC motor with a 70:1 metal gearbox and an integrated quadrature encoder that provides a resolution of 64 counts per revolution of the motor shaft, which corresponds to 4480 counts per revolution of the gearbox’s output shaft. These units have a 16 mm-long, 6 mm-diameter D-shaped output shaft. This gearmotor is also available without an encoder.
Key specifications:
voltage |
no-load performance |
stall extrapolation |
12 V |
150 RPM, 200 mA |
27 kg⋅cm (380 oz⋅in), 5.5 A |
Exact gear ratio: (25×30×28×40)/(10×10×12×10)=70:1
Dimensions
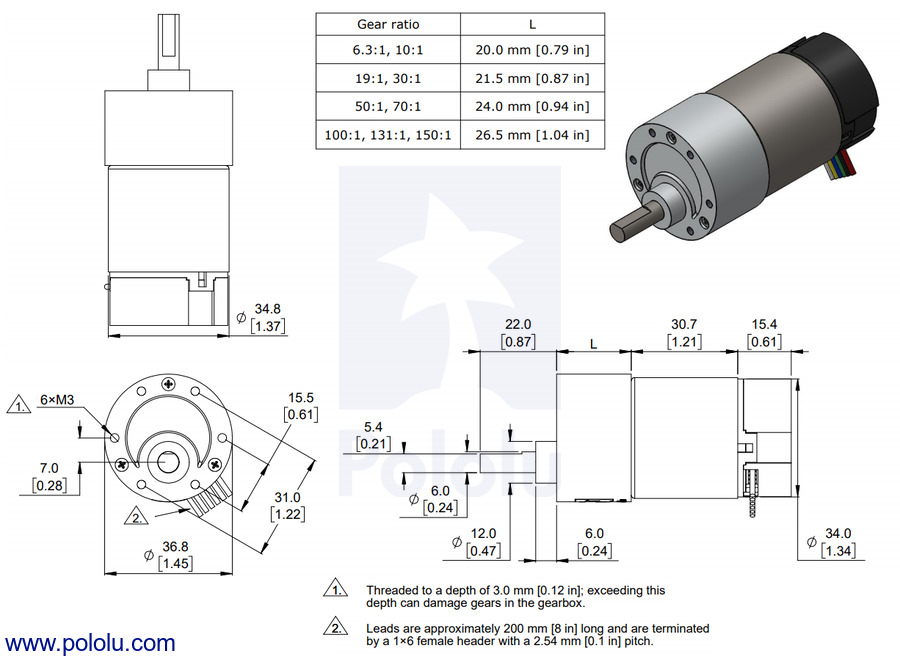 |
Dimensions of the 37D metal gearmotors with 64 CPR encoders. Units are mm over [inches].
|
This diagram is also available as a downloadable PDF (459k pdf).
Using the Encoder
A two-channel Hall effect encoder is used to sense the rotation of a magnetic disk on a rear protrusion of the motor shaft. The quadrature encoder provides a resolution of 64 counts per revolution of the motor shaft when counting both edges of both channels. To compute the counts per revolution of the gearbox output, multiply the gear ratio by 64. The motor/encoder has six color-coded, 8″ (20 cm) leads terminated by a 1×6 female header with a 0.1″ pitch, as shown in the main product picture. This header works with standard 0.1″ male headers and our male jumper and precrimped wires. If this header is not convenient for your application, you can pull the crimped wires out of the header or cut the header off. The following table describes the wire functions:
Color |
Function |
Red |
motor power (connects to one motor terminal) |
Black |
motor power (connects to the other motor terminal) |
Green |
encoder GND |
Blue |
encoder Vcc (3.5 – 20 V) |
Yellow |
encoder A output |
White |
encoder B output |
The Hall sensor requires an input voltage, Vcc, between 3.5 and 20 V and draws a maximum of 10 mA. The A and B outputs are square waves from 0 V to Vcc approximately 90° out of phase. The frequency of the transitions tells you the speed of the motor, and the order of the transitions tells you the direction. The following oscilloscope capture shows the A and B (yellow and white) encoder outputs using a 12 V motor at 12 V and a Hall sensor Vcc of 5 V:
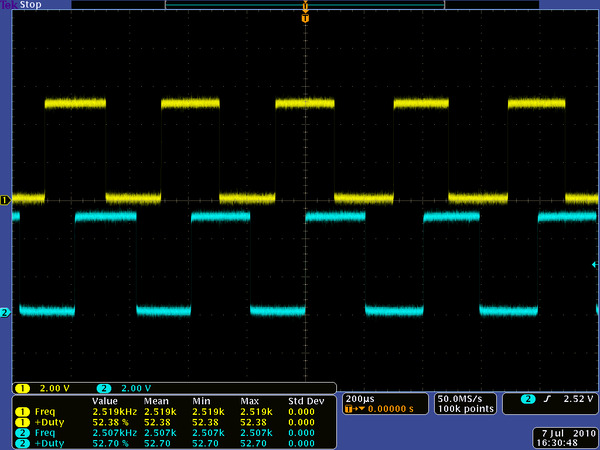 |
Encoder A and B outputs for 37D mm metal gearmotor with 64 CPR encoder (12V motor running at 12 V).
|
By counting both the rising and falling edges of both the A and B outputs, it is possible to get 64 counts per revolution of the motor shaft. Using just a single edge of one channel results in 16 counts per revolution of the motor shaft, so the frequency of the A output in the above oscilloscope capture is 16 times the motor rotation frequency.
Dimensions
Size: |
37D × 70L mm1
|
Weight: |
205 g |
Shaft diameter: |
6 mm2
|
General specifications
Gear ratio: |
70:1 |
No-load speed @ 12V: |
150 rpm |
No-load current @ 12V: |
0.2 A |
Stall current @ 12V: |
5.5 A3
|
Stall torque @ 12V: |
27 kg·cm3
|
Max output power @ 12V: |
10 W4
|
No-load speed @ 6V: |
73 rpm5
|
No-load current @ 6V: |
0.15 A5
|
Stall current @ 6V: |
3.0 A5
|
Stall torque @ 6V: |
16 kg·cm5
|
Motor type: |
12V |
Performance at maximum efficiency
Max efficiency @ 12V: |
52 % |
Speed at max efficiency: |
130 rpm |
Torque at max efficiency: |
3.2 kg·cm |
Current at max efficiency: |
0.68 A |
Output power at max efficiency: |
4.2 W |
General specifications
Lead length: |
20 cm6
|
Encoders?: |
Y |
Encoder resolution: |
64 CPR |
Notes:
-
1) Length measurement is from gearbox face plate to back of encoder cap (it does not include the output shaft). See dimension diagram for details.
-
2) D shaft.
-
3) Stalling is likely to damage the gearmotor. Stall parameters come from a theoretical extrapolation of performance at loads far from stall. As the motor heats up, as happens as it approaches an actual stall, the stall torque and current decrease.
-
4) This is the output power at the maximum recommended operating load of 10 kg⋅cm; higher power might be achievable for brief durations at higher loads (see performance graphs in the datasheet).
-
5) This motor will run at 6 V but is intended for operation at 12 V.
-
6) May vary by a few centimeters.